Production Optimization for Power Cable Manufacturing
• Published 9:00 AM EDT, Thu Jun 08, 2023
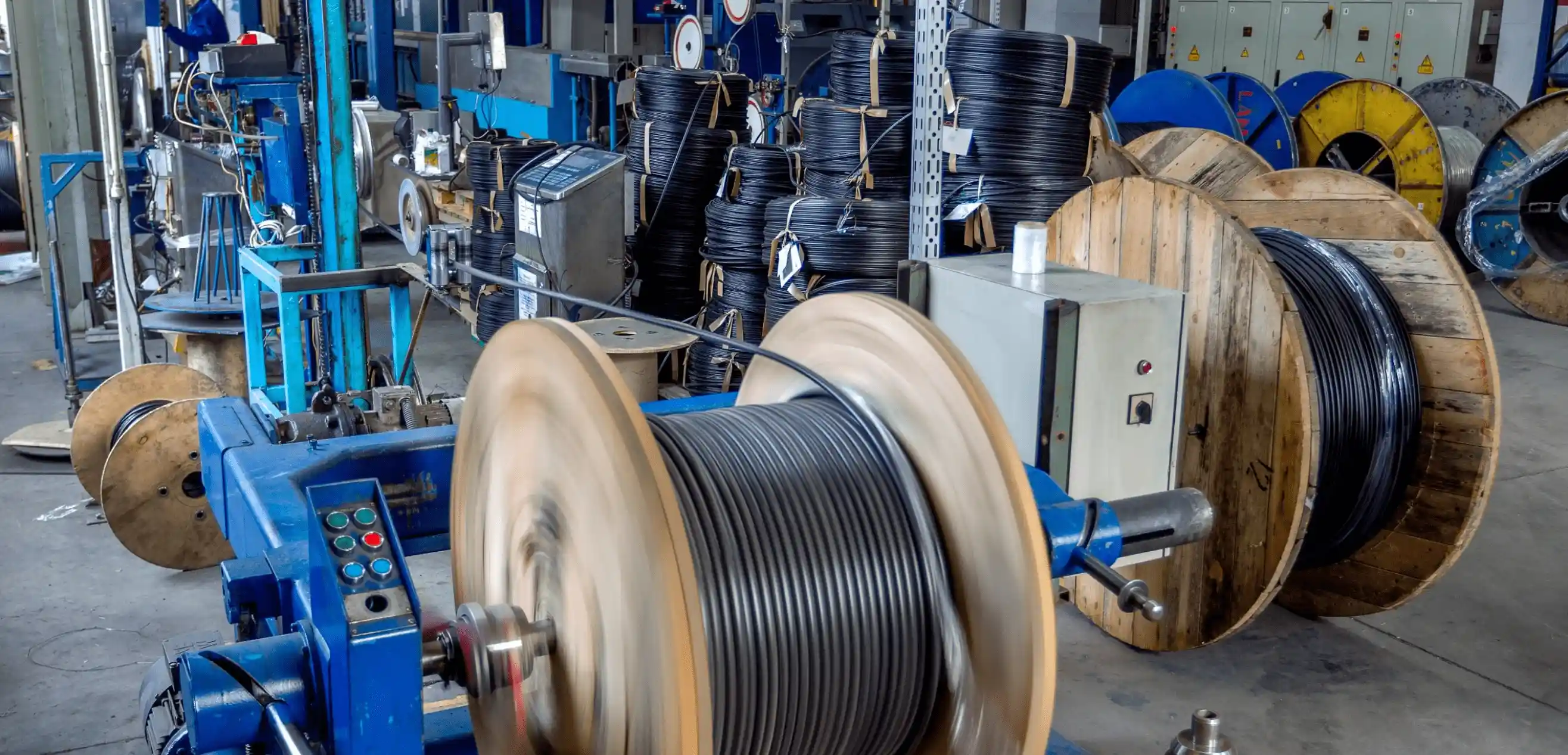
Cable manufacturing is a complicated process with multiple dependencies on raw materials, machines, and bobbins. Xeptagon IPS is an intelligent production scheduling system for manufacturing plants and factories, designed to manage process workflows that require highly intellectual decisions for higher throughput and optimal resource allocation. In the case of such decision-making, the IPS system impressively integrates machine availability, raw material management, partially processed stock management, flexible rescheduling, rush order handling, and various other aspects to generate realistic and optimized production schedules.
Realistic production floors face countless unforeseen events, bottlenecks, breakdowns, and simultaneous processes queued together with complex dependencies leading up to the final product output. Furthermore, busy manufacturing plants, such as wire production plants, are characterized by highly dependent processes that need careful handling; otherwise, multiple products may be delayed due to their interdependent nature.
Our system is an ideal solution for the aforementioned scenarios due to its simple user interface that allows users to implement complex process flows on their computers, with well-managed process parameters and flexibility to cope with unforeseen events with minimal user intervention. Among various features, the following process parameters are well-determined and evaluated through the system to automatically generate multi-scenario process schedules for users to select based on their preferences. Let’s delve deeper into a few features with wire manufacturing process integration in the IPS system.
- Sequential / Non-sequential Processes - The final output of a production line is linked back to raw materials through a chain of processes performed by various machines in both sequential and non-sequential manners. The connection between each process can be easily interpreted in the system by connecting nodes in the UI, just as the actual workflow is connected.
- Multi-assigning Machines to a Task - Large factories often have multiple machines capable of performing a specific task, such as wire winding, but with different performance ratings. Users can assign multiple machines and their specific parameters to a single task, and the system will generate multiple schedules and statistics according to the project timeline.
- Machine Configuration Setup - Different machines can perform the same process but with varying performance ratings. The system allows the addition of machine-specific parameters such as production speed, initial setup times, power consumption, and wastage, which are considered when that specific machine is utilized in the schedule.
- Input Material Ratios - For example, a wire twisting machine might produce 1 meter of red and black twisted wire using 1.5 meters of black wire and 1.2 meters of red wire. Users can enter such process-specific parameters to the task node, which will be utilized when scheduling the task.
- Concurrent Input of Materials - Continuing from the previous example, the system can consider how many wire bobbins of each input can be loaded into the machine as a machine-specific parameter to process in a single run without stopping.
- Concurrent Outputs - Each machine winds its twisted wires into bobbins in groups. The algorithm carefully evaluates such sequences to plan its successor task, ensuring it starts before fully completing the predecessor task.
- Loading and Unloading Time - Loading and unloading times of inputs and outputs are crucial factors that need to be accurately considered when a process is scheduled with a specific machine combination. Furthermore, users can customize these in-depth factors when generating a schedule through the Xeptagon IPS system.
- Simultaneous Process Planning - The complexity in scheduling highly dependent tasks arises when planning two consecutive tasks. The second task should start at its earliest available time slot and not be stopped due to the low output rate of the predecessor task. The algorithm can solve this in real time during project planning.
- Rush Order Handling - Orders with high market prices and tight deadlines can be integrated with already scheduled plans in two ways. The priority factor in production plans can be set to high, rescheduling lower priority production plans to accommodate rush orders.
- Partially Processed Stock Management - In addition to the above-mentioned method, partially finished stocks from previous production runs can be introduced to boost production speed, avoid bottlenecks, and stay on track with tight deadlines.
- Unforeseen Event Management - The system can handle real-time bottlenecks caused by machine breakdowns, power failures, and various other events. Each schedule can be paused and restarted after such events by following a simple rescheduling flow, then continuing with a new schedule to complete the remaining production and deliver with minimal impact on deadlines.
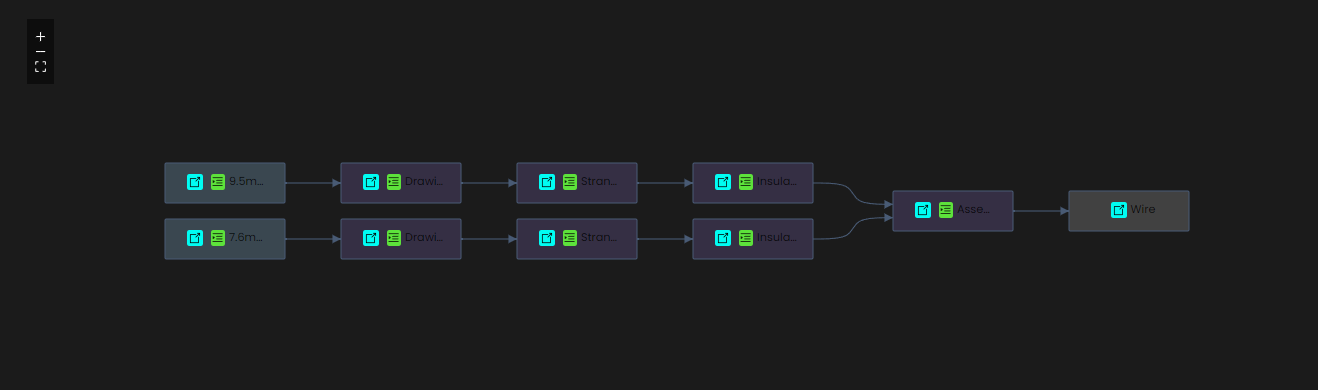
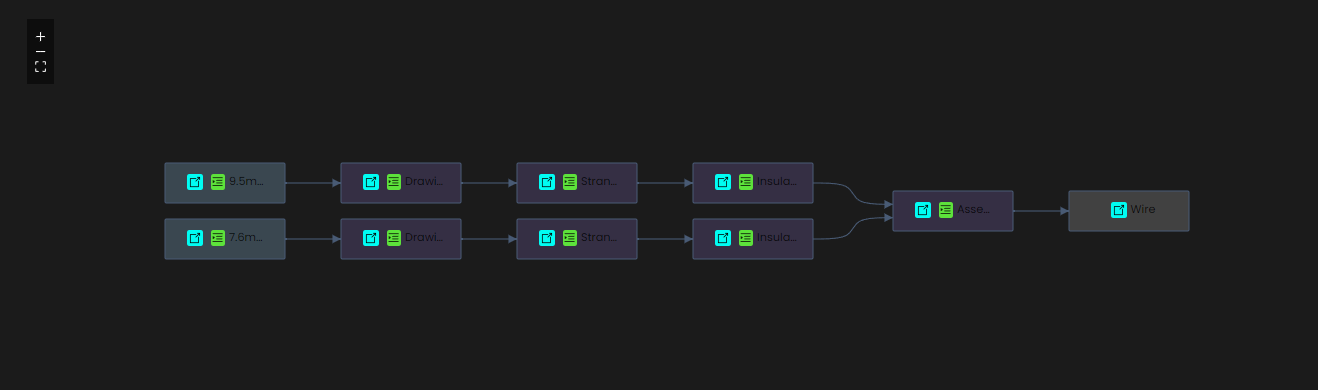
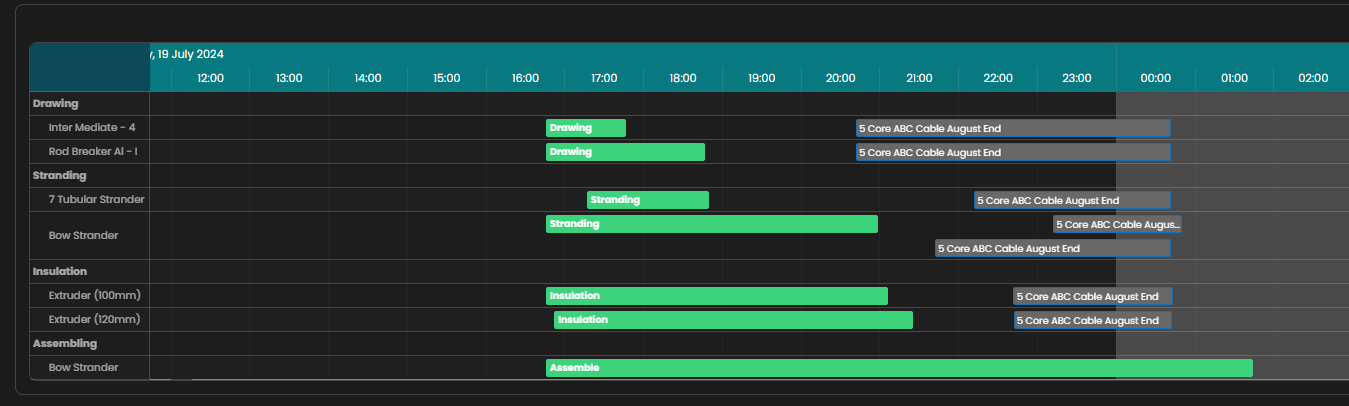
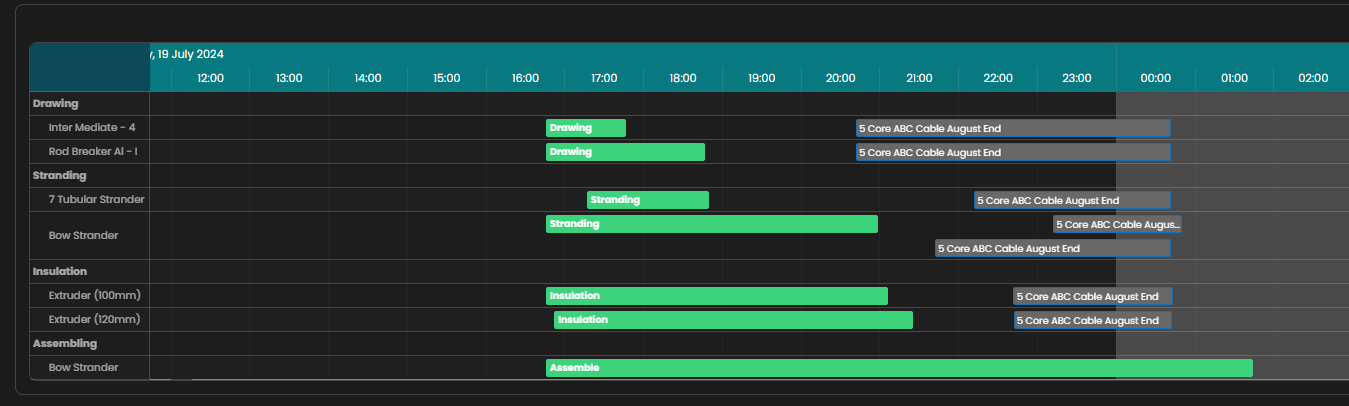
The system is currently tested in the manufacturing plants of Sierra Cable PLC, a listed company in the Colombo Stock Exchange (CSE) with manufacturing facilities in Sri Lanka, Africa and Fiji.