Data-Driven Chiller Plant Optimization by Xeptagon
• Published 9:00 AM EDT, Thu Jun 15, 2023
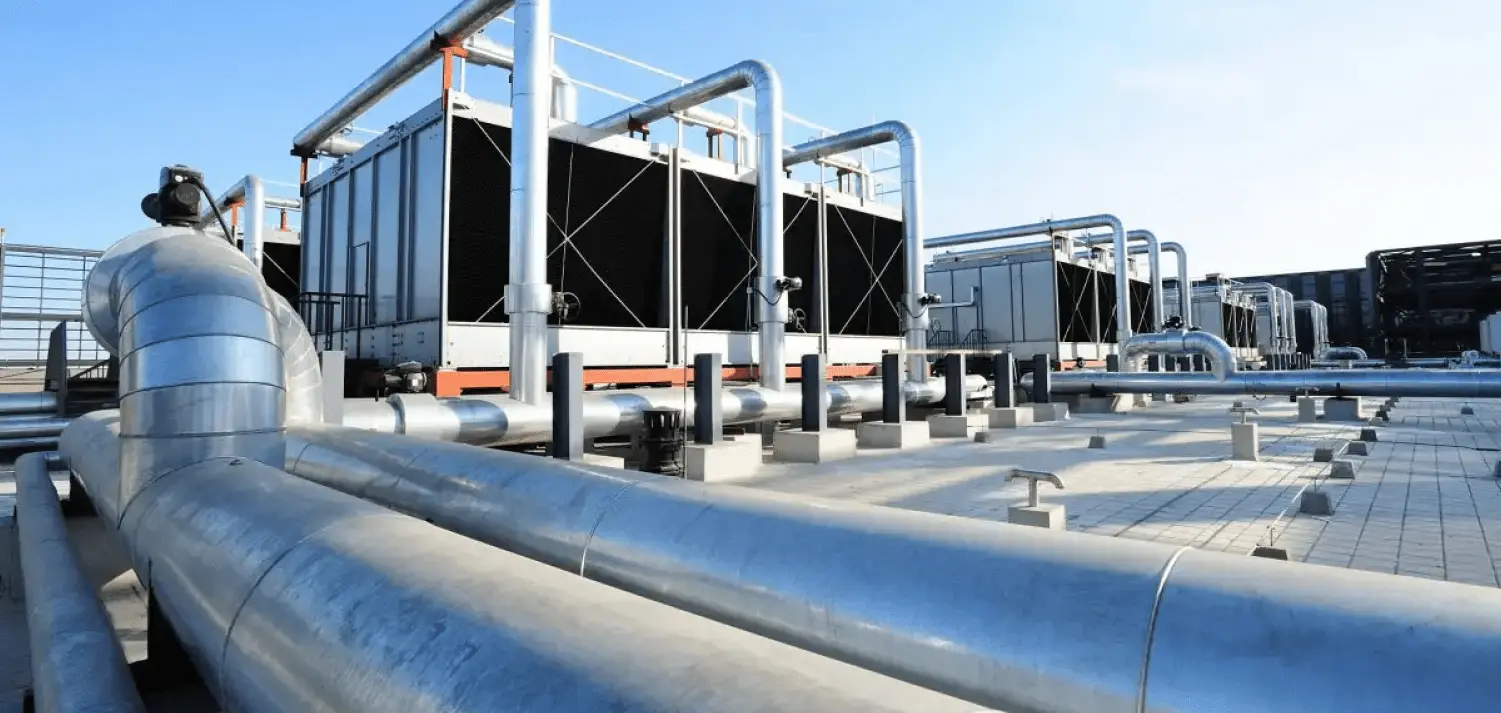
Electrical energy requirement for air conditioning and space cooling subsystems of Building Management Systems (BMS) has increased at 4% of average steps per year since 2000, doubling as the increment compared to water heating and lighting subsystems. Air conditioning and space cooling subsystems account for approximately 20% of total BMS electricity consumption or 10% of global electricity consumption according to the International Energy Agency (IEA). As identified, within the BMS and air conditioning subsystem, chiller plants are the most energy-intensive component that needs to be optimized to improve performance to reduce energy costs with increasing cooling demand.
A chiller is the main component in an air conditioning system that changes the temperature of a cooling liquid whose temperature is controlled by a refrigerant cycle and capable of supplying a chilled liquid stream continuously while circulating it through the device. There can be multiple chillers of different capacities and technologies within a chiller plant with different overall system configurations.
Most modern commercial chiller plants consist of multiple chiller units with different individual capacities in parallel configurations other than series and composite configurations. When it comes to the operating strategy, the sequencing strategy is commonly used to operate multiple chillers to supply chilled water for fulfilling daily cooling demand. The sequencing strategy is based on conventional mechanical systems and equations built on oversimplified assumptions which change the on/off condition of chiller units to cover instantaneous cooling demand. The conventional sequencing strategy is sub-optimal, more focused on supplying the instantaneous cooling demand with a minimum number of chiller units in operation rather than operating it most efficiently.
Data-driven chiller plant optimization methods are giving promising results when it comes to improved efficiency, energy saving and minimized machine ageing through a proper combination of modern machine learning techniques and air conditioning domain expertise. Research-based advanced chiller sequencing algorithm with real-time data acquisition and cooling load prediction method shows the highest energy saving among other optimization methods.
As a technical overview of the above-mentioned method, the daily cooling demand forecast is populated for the next 24 hours using a machine learning model based on historical data and other environmental factors as input for optimal sequencing and various set point selection algorithm, which is constructed as a graph optimization problem, generates optimal sequence and set points under restrictions of minimum cooling fluctuations, uptime/downtimes and other critical constraints. Also, this optimization method is based on dynamic data coming from modern Internet of Things (IoT) systems or integrated sensor systems for real-time optimization.
The major benefit of applying data-driven optimization on a chiller plant is its capability of performing well in dynamic environments and varying parameters which are extremely difficult to model using a physical mechanical system since its dynamic behaviour. Data-driven systems are highly capable of handling such scenarios and are compatible with physical systems. These optimization methods are more focused on optimizing existing resources rather than implementing another set of physical resources.
The investment in data-driven chiller plant optimization systems is much more cost-effective compared to installing new chiller plants or spending a high amount on maintenance due to avoidable machine ageing. As for the reference, research work and simulations done on the above data-driven chiller optimization method proved that it can be outperformed the conventional chiller sequencing method through entire cooling demand and cause 25% of energy savings, depending on the efficiency of the conventional chiller sequencing method.
Xeptagon is currently undergoing an initial assessment of a chiller plant optimization project for a large shopping mall complex in Hong Kong. The goal is to use IoT-coupled data-driven optimization techniques to reduce energy costs.
Need to Optimize your Chiller Plant to Save on Energy Costs?? Contact us at info@xeptagon.com
Need to Optimize your Chiller Plant to Save on Energy Costs?
Get in touch with us!